
Flexible Packaging
Flexible packaging is one of the largest and fastest growing markets in the global packaging industry, driven by the fact it is a convenient and economical way to preserve, distribute, and package food items. As collective ambition for the circular economy expands, producers of flexible packaging need to be agile in their product innovation to maximize this opportunity. Partnering with innovative suppliers along the supply chain is key part to this agility.
At H.B. Fuller, our team of industry experts develop flexible packaging adhesives that address the ever-changing and rigorous requirements of the flexible packaging industry.
From in-house assessments and demonstrations with our complete range of laminating adhesives, we have the solutions you need to achieve your business goals. Our new range of Flextra™ compostable lamination adhesives are enabling packaging manufacturers to produce certified compostable packaging, ideal for food packaging where food contamination makes it difficult to recycle.
Our comprehensive line of flexible packaging solutions and materials includes Flextra™ solvent-free and solvent-based adhesives for film, paper and foil laminating and hot melts for heat seal applications, in-mold-labeling, and laminating and coating waxes.
Our extensive product portfolio covers many flexible packaging structures:
- Film/Film laminations (film/film laminations, film/board/film laminations, film/foil laminations, wax/foil laminations)
- Side and End Seam adhesive (paper/paper lamination, paper/film lamination, wax/foil lamination, bottom paste adhesive, side seam adhesive, heat seal)
- Surface print or monoweb film (heat seal and wax coatings)
And end food applications:
- Form fill and seal packaging
- Pouches (ambient and retort)
- Overwrap and protective packaging
- Microwave packaging (susceptor pads, food trays, conventional oven packaging, foil laminating)
- Sustainable end of life packaging
-
Compostable Adhesives for Flexible Packaging
Consumer concerns about single use flexible packaging on the environment is growing. As a result, the flexible packaging industry is focused on addressing end-of-life issues, such as recyclability and composability.
Flexible packaging companies are seeking new ways to develop more sustainable products and H.B. Fuller compostable adhesives are enabling sustainable packaging to become a reality.
In addition to being a more sustainable option versus traditional solvent-based adhesives, benefits of compostable adhesives include:
- Minimizes stress on the ecosystem
- Reduces costs of waste processing
- Keeps manufacturers ahead of regulatory changes
H.B. Fuller offers Flextra™ compostable adhesive solutions for the flexible packaging market. These products work seamlessly with existing equipment. In industrial composting facilities, the adhesives decompose with no toxic residue, microplastics, or other pollutants. They have similar performance to conventional multi-layer packaging adhesives, good appearance and adhesion, and can be utilized on standard equipment.
-
Recyclable Adhesives for Flexible Packaging
Flexible packaging, enabled by laminating adhesives, offers benefits in material efficiency and design flexibility. Recyclability is one of the key drivers of sustainability in the flexible packaging industry. Collaboration and openness to evolving technologies are crucial for achieving sustainability goals across the value chain. Our Flextra® SBA 5250 + XA 3350 laminating adhesive is now approved by RecyClass in Europe as fully compatible with the polypropylene flexibles recycling stream. It meets FDA and EU food safety regulations compliance (FDA 177.1390), is free from substances of concern, and offers superior bonding properties and room temperature cure. This innovative solution shows our commitment to providing the market with sustainable solutions.
-
Food Safe Adhesives for Flexible Packaging
Food waste reduction is a value of flexible packaging.
H.B. Fuller’s global line of Flextra™ adhesives safely protect food as it moves throughout the supply chain. The Flextra™ range includes both solvent-based and solvent-free products for medium- and high-performance applications. Individual solutions offer additional benefits, such as room temperature curing, fast curing and PAA decay, as well as the option to use an aliphatic system to avoid PAA altogether.
FlexPack Epoxy Silane-Free
We are taking a proactive approach to the anticipated European Commission regulation on epoxy silanes with our epoxy silane-free adhesives for flexible packaging. In addition, we have carefully reviewed our adhesive formulations, removing other undesired substances. We can offer expert regulatory advice for your adhesive selection in Europe and around the globe.
-
Reduce Ink Smear During Lamination
Every flexible packaging producer wants to ensure their laminated construction is consistently produced to a high quality, including the quality of the printed brand graphics.
In today's competitive environment, brand graphics have a significant narrative to convey for the Consumer Packaged Goods companies (CPGs). They attract attention. They distinguish the CPG on the supermarket shelf from competitors, creating a first and lasting impression. It is critical that graphics and logo are spotless and ink smear* free to generate a great brand experience.
At H.B. Fuller, our research and development scientists have designed an adhesive technology for converters who have experienced difficulties with ink and adhesive interactions and are searching for decreased waste and minimal flaws.
-
Retort Flexible Packaging Adhesives
Retort technology is a thermal processing technique that preserves food and increases shelf life, and its use continues to increase with the growing number of ready-to-eat meals supplied in pouch style flexible packaging.
The retort process involves the super-heating of food in the package using direct or indirect steam to create the heat. Traditional flexible packaging lamination adhesives formulated to withstand the demanding retort conditions are predominately solvent-based adhesives. Many of these contain polyesters and other chemicals to improve bonding performance and reduce curing times. However, these chemicals are also analytes of concern with respect to food safety regulations, with the regulations stating migration thresholds for each. The solvent carrier needs to be evaporated and the fumes recovered, which is a costly and energy intensive part of the operation. The laminated material must be cured before use and curing times and conditions vary widely from two days storage at 50°C, right through to 14 days in ambient conditions.
Next Generation Adhesive Technology
At H.B. Fuller, our scientists thrive on challenges. When tasked with developing a high performance, food safe adhesive for the retort pouch market, they more than answered the challenge. Moving away from old technology, our team of scientists developed a pure aliphatic adhesive solution, specifically designed for retort applications up to 275°F / 135°C.
-
Technical Expertise
The collaboration with our customers helps us better understand market trends and assist you in delivering consumer and durable goods that enhance lives. We can recommend process adjustments for ink smear by identifying what must be modified, such as a longer or hotter dry time, or an adhesive change, and we can test film and adhesive combinations. Our Technology Centers of Excellence are located all over the world and connect our adhesive technology and market specialists to our customers' product design and development experts. Here, we can test your substrate with advanced analytics to provide you with the adhesive that best meets your specific processing requirements and without causing downtime at your facilities.
In our global headquarters, we have a Nordmeccanica Super Combi 3000 Laminator that runs the full Flextra™ line of solvent-based, solvent-free and water-based laminating adhesives. With web widths of 20’ to 50’, line speed of up to 1300 feet per minute and primary and secondary in-line corona treatment.
Both facilities enable our customers to evaluate new adhesives without interrupting their production lines and:
- Complete lamination testing for your evaluation and development needs
- Schedule a trial at your own convenience without the need to break into your production schedule
- Evaluate actual production films, using your commercial rolls and sealant films
- Cure laminated rolls between 60°F and 100°F in our specially built temperature-controlled room
- Optimized solution at our facility eliminates 'trial fatigue' from suppliers guessing which adhesive will work
- Produce large rolls as needed for slitting, pouching, and filling
H.B. Fuller is a global adhesives provider with a comprehensive range of solutions for all your flexible packaging needs, including laminating, food packaging and displays. Contact us today to discuss more about your flexible packaging requirements.
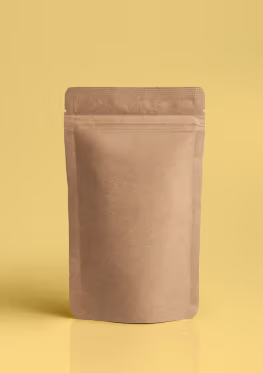